How We Support You in Picking the Perfect Mold Upender
Choosing the right Mold Upender is a critical decision for any manufacturing process, especially when it directly impacts your efficiency, safety, and cost-effectiveness. Whether you’re looking to streamline your production line, ensure the safe handling of heavy molds, or meet strict industry standards, the Mold Upender you choose plays a pivotal role. At FHOPEPACK, we understand the importance of this decision, and we are committed to supporting you throughout the entire process—from selection to integration.
Our goal is to make your Mold Upender selection as smooth and informed as possible. By offering a range of tailored solutions, clear financial insights, and ongoing support, we ensure that your choice not only meets your immediate needs but also supports long-term growth and operational efficiency.
As your partner, FHOPEPACK is here to walk you through every step of the journey. From providing detailed product specifications to offering personalized guidance, we strive to make your decision process both seamless and successful. Below, we’ll explore how we support you in picking the perfect Mold Upender for your production goals.
1. Which aspects of our Mold Upender are tailored to suit your production goals?
Understanding the unique needs of your production line is the first step in selecting the right Mold Upender. FHOPEPACK offers a variety of customizable features to ensure our Mold Upender meets the specific demands of your manufacturing process. Whether you’re handling large, heavy molds or require high-speed operation, our machines are designed to support your goals with precision and reliability.
The customization options available for the Mold Upender allow us to align the equipment’s capabilities with your production goals. From lifting capacities to operational speeds, every feature is designed to boost efficiency and minimize downtime. But it’s not just about meeting current needs—it’s about future-proofing your operations as well.
Customizable Features for Maximum Efficiency
FHOPEPACK’s Mold Upender can be tailored in several key areas to meet specific production demands:
Lifting Capacity: Whether you’re working with heavy-duty molds or lighter components, we offer a wide range of lifting capacities. The flexibility to choose the right lifting power ensures your machine can handle your heaviest molds safely.
Speed and Precision: Speed is essential in a high-output production line. Our machines are engineered for quick operation without sacrificing the precision needed to avoid mishandling.
Footprint and Integration: Space is often at a premium in many facilities. We design our Mold Upenders with a compact footprint, making it easier to integrate them into existing production lines, without sacrificing performance.
The ability to tailor the Mold Upender to fit the exact requirements of your production line ensures that you receive the maximum benefit from the machine, helping you improve productivity while keeping costs manageable.
Feature | Benefit | Customization Options |
---|---|---|
Lifting Capacity | Handles different mold sizes and weights | Various ranges available |
Operational Speed | Increases throughput without compromising quality | Adjustable speed settings |
Compact Design | Saves valuable space in your production area | Customizable to fit layout |
These customizations mean that your Mold Upender isn’t just another machine—it’s a strategic asset designed specifically for your production environment.
Choosing the Right Mold Upender for Your Goals
By considering all of these aspects, FHOPEPACK ensures that your Mold Upender is perfectly suited to your operational needs. The goal is to help you achieve greater efficiency, improved safety, and higher throughput, ultimately optimizing your bottom line.
2. What makes our experience and reputation key to forming a strong and reliable partnership?
When choosing a supplier for equipment as critical as a Mold Upender, experience matters. FHOPEPACK’s 15 years of experience in the packaging machinery industry have shaped us into a trusted and reliable partner for businesses worldwide. Our deep knowledge of manufacturing needs, combined with a commitment to quality, positions us as the ideal partner for businesses seeking long-term solutions.
Experience isn't just about years in business; it’s about understanding the intricacies of your production line, identifying potential challenges, and delivering solutions that add real value. With FHOPEPACK, you’re not just purchasing machinery—you’re gaining a partner dedicated to supporting your growth.
FHOPEPACK’s Track Record of Excellence
For over 15 years, we’ve designed and supplied packaging machinery to clients across various industries, including automotive, steel, and manufacturing. This broad experience allows us to provide unique insights and advice, ensuring you receive a solution that aligns with your operational goals.
We have built a reputation for delivering high-quality machines that stand the test of time. Our clients return to us year after year because they know they can rely on us to provide not just a machine, but a comprehensive, well-thought-out solution that integrates seamlessly into their operations.
Why Trust FHOPEPACK?
Industry Experience: Over a decade of experience in designing, manufacturing, and supporting packaging machinery.
Customer-Centric Approach: We focus on understanding each client’s unique needs and challenges, offering tailored solutions.
Proven Reliability: Our machines are known for their durability, efficiency, and minimal downtime.
This experience gives you the confidence that FHOPEPACK will provide the right Mold Upender for your needs while ensuring your investment is backed by ongoing support and service.
3. What detailed cost breakdowns can we offer to help you evaluate ROI effectively?
Investing in a Mold Upender is a significant commitment, and understanding the total cost of ownership is essential for making a sound business decision. At FHOPEPACK, we provide detailed cost breakdowns that help you evaluate the return on investment (ROI) for the Mold Upender, ensuring transparency and helping you plan for the long term.
Our cost breakdown covers all aspects of the Mold Upender purchase, from initial pricing to ongoing operating costs, allowing you to calculate your ROI effectively and confidently.
Transparent Pricing for Better ROI Evaluation
We believe that understanding the total cost of ownership is crucial to making an informed decision. Our pricing breakdown includes:
Initial Purchase Price: Competitive pricing for the Mold Upender, based on your customization needs.
Operating Costs: Energy-efficient designs that help minimize long-term operating expenses.
Maintenance Costs: Optional service plans to ensure your Mold Upender stays in peak condition with minimal maintenance costs.
Potential Savings: Long-term savings due to increased productivity, reduced labor, and minimized material waste.
These components allow you to see the full financial picture, ensuring you understand not just the upfront cost but also the potential savings and ROI over the machine’s lifespan.
Cost Breakdown | Estimated Cost | Explanation |
---|---|---|
Initial Purchase | $9,000 | Based on selected specifications |
Operating Costs | $12,000 per month | Energy-efficient features |
Maintenance Costs | $1500 per year | Service plans available |
Long-Term Savings | 20%+ | Reduced labor and material waste |
These transparent breakdowns help ensure that your Mold Upender investment is a sound financial decision, with clear savings and a return that justifies the initial expense.
4. What makes our comprehensive after-sales support essential for smooth operational continuity?
After making an investment in a Mold Upender, the next crucial factor to consider is ongoing support. FHOPEPACK understands that smooth operational continuity depends on reliable after-sales service. Our commitment extends well beyond the installation phase; we ensure that your Mold Upender runs at its best throughout its lifecycle.
Comprehensive After-Sales Support
Machine Delivery & Setup: No need to worry about dismantling; we offer fast, efficient delivery and setup services. Our design minimizes installation complexity, with only power and air connections required.
Online Troubleshooting: Our expert support team is available online to help resolve any issues, no matter where you are.
On-Site Commissioning: We provide on-site commissioning to ensure the machine is correctly installed and optimized for your specific needs.
Warranty & Spare Parts: Our products come with a comprehensive warranty, and we supply genuine spare parts for easy replacements.
Training & Consultation: We offer in-depth training to your team, ensuring they are fully prepared to operate the machine efficiently.
These services ensure minimal downtime and maximum performance from your Mold Upender.
Support Table
Service | Details |
---|---|
Delivery & Setup | Fast delivery, no dismantling required |
Online Troubleshooting | 24/7 online support |
On-Site Commissioning | Professional setup and optimization |
Warranty & Spare Parts | Full warranty and access to genuine parts |
Training & Consultation | On-site training for seamless integration |
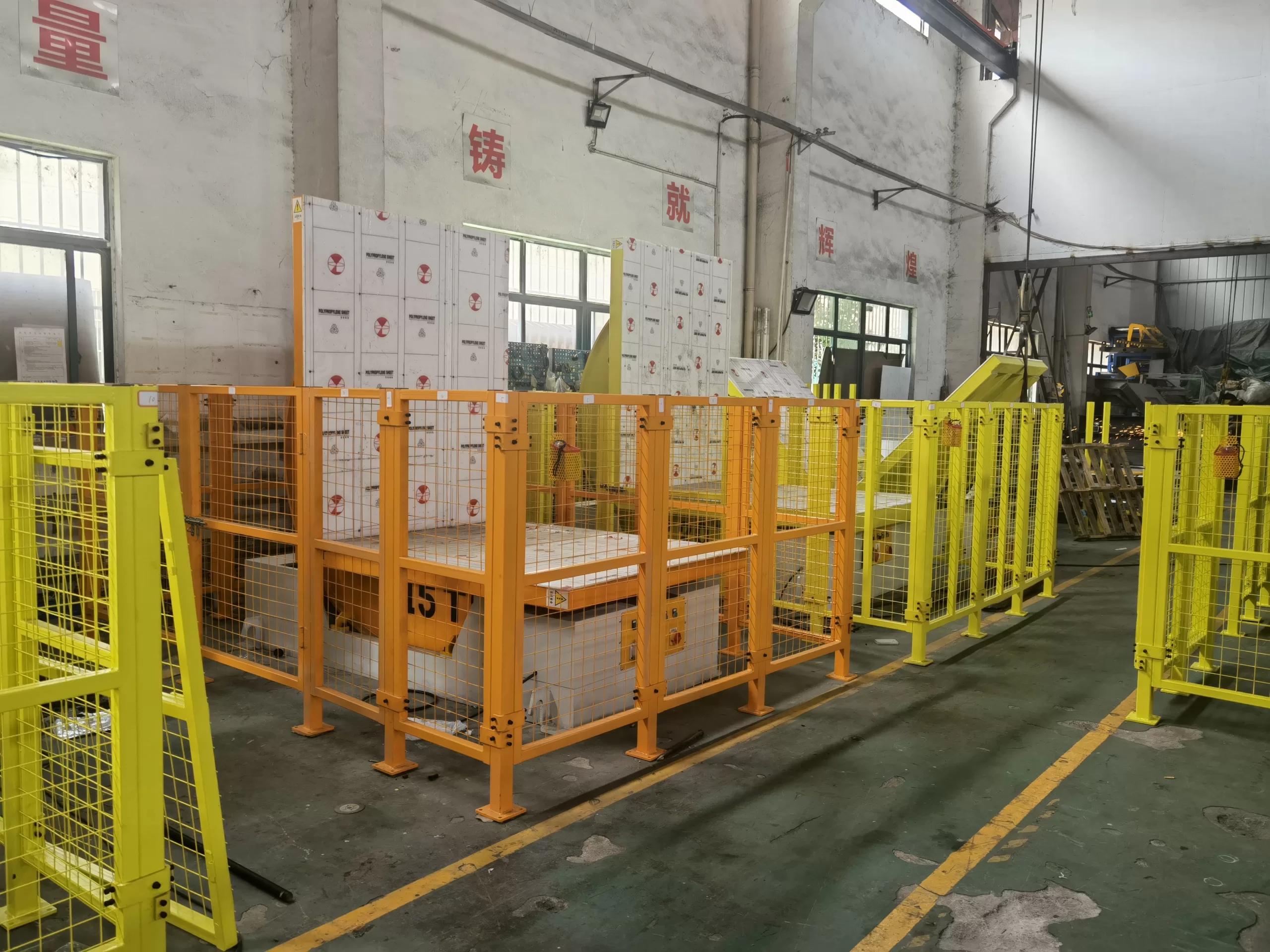
5. What design features enable our Mold Upender to exceed safety and compliance standards?
Safety is a top priority when selecting industrial machinery. FHOPEPACK’s Mold Upender is designed to exceed all safety and compliance standards, ensuring both operator safety and regulatory adherence.
Safety Features Built into the Mold Upender
Our Mold Upender is equipped with the latest safety features:
Safety Fence: A protective fence around the machine to prevent accidental contact with moving parts.
Light Beam: A light curtain system that detects obstacles and stops the machine to prevent injury.
Sensors: Equipped with sensors to automatically halt the machine in case of a malfunction or safety hazard.
Emergency Stop Buttons: Easily accessible emergency stop buttons in case of an urgent need.
These features not only protect operators but also ensure your business meets all safety compliance requirements.
6. What kind of training and support do we offer to make the integration process hassle-free?
At FHOPEPACK, we understand that seamless integration of new machinery into your existing production line is crucial. That’s why we provide comprehensive training and support to ensure that the Mold Upender integrates effortlessly into your operations. Our goal is to make the process as smooth and efficient as possible, so you can maximize productivity from day one.
Training and Integration Support
Hands-On Training: We offer detailed hands-on training sessions for your operators, ensuring they understand the machine’s functions and maintenance requirements.
Remote Assistance: If you need help post-installation, our team provides remote support via video calls or online chat.
Integration Planning: Our engineers work closely with you to plan and design the integration process, minimizing any disruption to your production flow.
Documentation & Guides: You’ll receive comprehensive manuals and step-by-step guides that outline all machine operations, safety protocols, and maintenance schedules.
Regular Follow-ups: We schedule follow-up calls and visits to ensure that everything is running smoothly, and provide advice on performance optimization.
Support Table
Training & Support Service | Details |
---|---|
Hands-On Training | Practical training for machine operation |
Remote Assistance | Access to remote troubleshooting support |
Integration Planning | Assistance in planning seamless integration |
Documentation & Guides | Comprehensive machine operation manuals |
Regular Follow-ups | Periodic check-ins and performance advice |
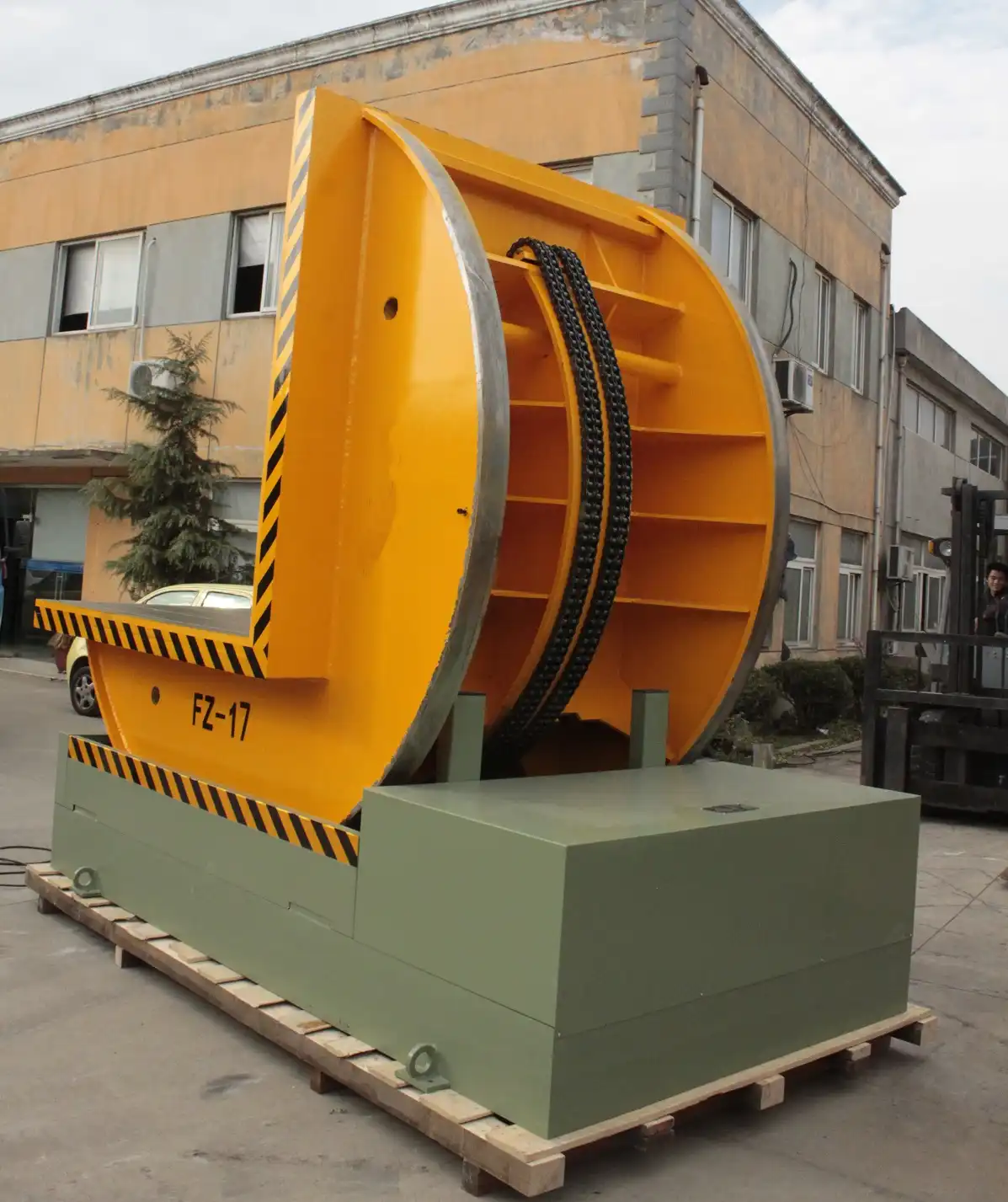
7. What steps do we take to personalize and future-proof our Mold Upender for your business expansion?
At FHOPEPACK, we recognize that every business is unique and that your operational needs may evolve over time. That's why we offer personalized solutions that are adaptable to future business growth. Our Mold Upender is designed with flexibility in mind, so it can evolve alongside your business.
Personalization and Future-Proofing
Customization Options: Based on your specific production needs, we offer customizable features such as size adjustments, speed control, and load capacity.
Modular Design: The Mold Upender is built with modular components that can be upgraded as your production scale increases.
Industry 4.0 Compatibility: Our machines are ready to integrate with Industry 4.0 technologies, such as automated data collection and real-time performance monitoring.
Scalable Systems: As your production volume grows, our Mold Upender can easily scale up to meet higher demands without the need for a complete overhaul.
Future-Ready Features: We keep an eye on emerging industry trends and incorporate forward-thinking features to make sure our machines stay relevant for years to come.
These steps ensure that your Mold Upender is not just a solution for today, but a partner in your long-term business success.
8. What makes our delivery timelines and installation services reliable and straightforward?
At FHOPEPACK, we know that time is crucial, especially when it comes to machine delivery and installation. That's why we’ve streamlined our delivery and installation process to be as fast and efficient as possible. Our commitment is to ensure that your Mold Upender is up and running with minimal delays, so you can maintain your production schedule.
Efficient Delivery and Installation Process
Fast Delivery: We keep a stock of Mold Upenders ready for immediate dispatch. With a delivery time of 3-5 days, we can get your machine to you quickly.
Simple Installation: Our Mold Upender is designed for easy installation. All you need to do is unpack, connect power and air supplies, and you're ready to start. Our machines come with a free installation design to minimize the time and effort required for setup.
Video Guides and Manuals: We provide step-by-step video guides and manuals to assist with installation. This ensures that your team can follow a clear, straightforward process without the need for external help.
On-Site Support: While the machine installation is designed to be simple, our engineers are available to provide on-site support if needed, ensuring everything runs smoothly from the start.
Delivery & Installation Timelines
Service | Timeline/Details |
---|---|
Delivery | Machines in stock, 3-5 days delivery time |
Installation | Unpacking, power and air connection required |
Support | Video guides and manuals for setup |
On-Site Assistance | Available for installation assistance |
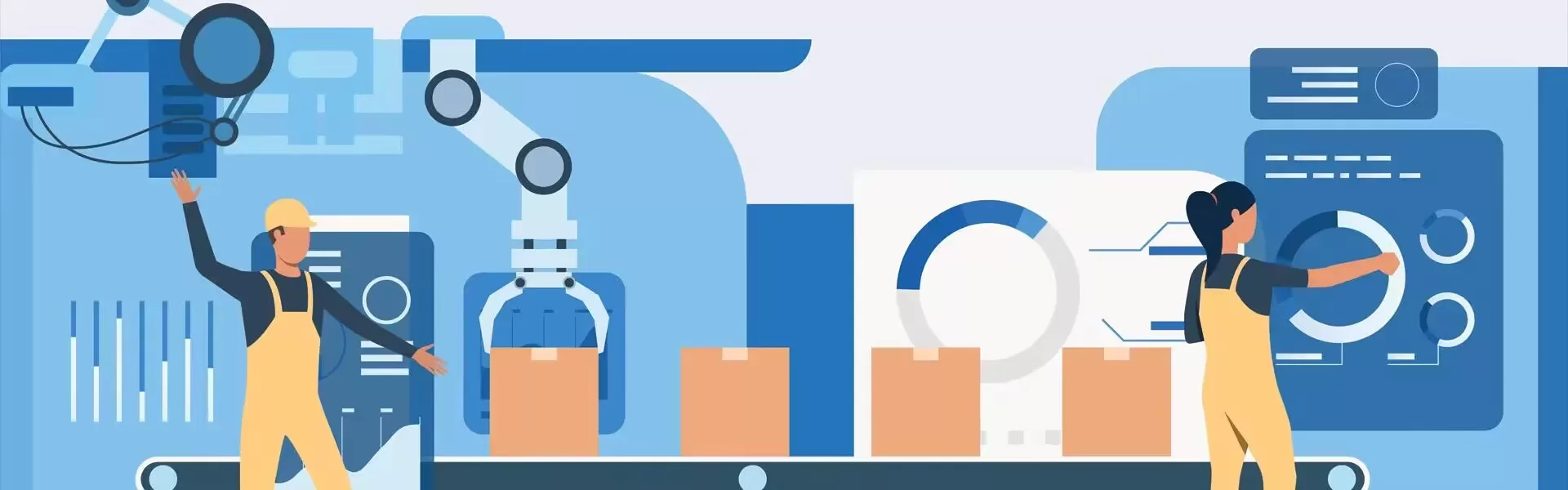
9. What makes our success stories and case studies effective in building trust with our clients?
At FHOPEPACK, we believe that real-world examples are one of the best ways to showcase the value and reliability of our products. Our success stories and case studies are not only a testament to the quality of our Mold Upender but also serve as proof of our commitment to delivering customized, effective solutions to meet our clients' needs.
Proven Success
Client Testimonials: We have received outstanding feedback from clients who have successfully integrated our Mold Upender into their operations, highlighting its reliability, efficiency, and ease of use.
Case Studies: We regularly publish detailed case studies, outlining how our Mold Upender has solved specific challenges in various industries. These case studies demonstrate how our product has helped companies improve their processes, reduce costs, and increase productivity.
Client Partnerships: Over the years, we’ve built long-lasting relationships with many clients, becoming their trusted partner for packaging and automation solutions.
ROI Demonstration: Many of our case studies focus on the return on investment (ROI) our clients have experienced after integrating the Mold Upender, providing clear, measurable results that showcase the product’s impact.
Case Study Highlights
Client/Industry | Challenge | Result |
---|---|---|
Automotive Manufacturing | High production costs and low automation | Reduced labor costs by 25%, improved efficiency by 30% |
Construction Industry | Inconsistent mold handling and risk of damage | Increased production speed by 20%, eliminated mold damage |
Steel Coil Production | Complex handling of large molds | Streamlined production process, improved safety |

10. What features of our flexible contract terms help protect and maximize your investment?
When it comes to making significant investments in machinery, having flexible and transparent contract terms is essential. We understand that every business has different needs, and that’s why we offer tailored contract options to suit your requirements. Our goal is to ensure that your investment in our Mold Upender is not only protected but also maximized for long-term value.
Flexible Payment Options
Customizable Payment Plans: Whether you prefer to pay upfront or spread the cost over time, we offer flexible payment plans to fit your financial situation.
Lease-to-Own Options: For businesses that may not have immediate capital, we offer lease-to-own contracts that allow you to pay over time while still enjoying the full benefits of our equipment.
Extended Warranty: We provide extended warranty options to give you peace of mind, ensuring your machine is covered for any unexpected repairs or maintenance.
Contract Flexibility
Adjustable Delivery Schedules: We understand that timing can be critical for your operations, so we offer adjustable delivery schedules to match your production timeline.
Service and Maintenance Agreements: Our flexible service agreements ensure that you can opt for ongoing support, ensuring that your Mold Upender continues to perform at its best throughout its life cycle.
Performance Guarantees: We back our products with performance guarantees, which means that if your Mold Upender doesn’t meet the agreed-upon specifications, we’ll work with you to resolve the issue.
Why Flexible Contracts Matter
Feature | Benefit |
---|---|
Custom Payment Plans | Fit your financial situation |
Lease-to-Own Options | Acquire equipment without upfront cost |
Extended Warranty | Protect against unexpected repair costs |
Adjustable Delivery | Ensure timing matches production needs |
Performance Guarantee | Guarantee product performance |

Conclusion
At FHOPEPACK, we are dedicated to supporting your business every step of the way, from choosing the perfect Mold Upender to ensuring its seamless integration into your production line. With flexible contracts, reliable delivery, comprehensive support, and a proven track record, we’re here to help you achieve maximum value from your investment and elevate your operational efficiency.